Ce cours traite les techniques de détections des défaillances les plus utilisées en industrie à savoir l’analyse vibratoire, la thermographie infrarouge, le contrôle ultrasonore, les contrôles non destructifs et l’analyse des huiles. En effet toutes les machines, et particulièrement les machines tournantes, vibrent et l'image vibratoire de leurs vibrations a un profil très particulier lorsqu'elles sont en état de bon fonctionnement. Dès que des phénomènes d'usure, de fatigue, de vieillissement, de désalignement, de balourd, etc. apparaissent, l'allure de cette image change, ce qui permet, de quantifier l'intervention. La plupart des défauts mécaniques peuvent être détectés par cette technique. La thermographie est une des techniques utilisées pour contrôler l'état des structures et des systèmes industriels. Elle mesure l'intensité des émissions de rayons infrarouges (c'est-à-dire de chaleur) par une caméra infrarouge, afin de déterminer les conditions opératoires de l'équipement. Tout mouvement relatif entre pièces produit des ultrasons de friction. La mesure et l'enregistrement des signaux ultrasonores effectués à cadence régulière, et leur suivi dans le temps permettent de détecter beaucoup de problèmes de façon simple efficace et peu coûteuse. Les contrôles non destructifs ont pour objectifs de détecter les défauts matière, les défauts de fabrication et les défauts dus à la fatigue (fissuration) qui ne sont pas détectables visuellement et qui occasionnent des casses du matériel. Ils permettent de suivre l’évolution de ces défauts (vitesse de propagation) et de changer la pièce juste avant que la pièce ne casse. Les analyses systématiques des huiles des circuits permettent de détecter toute anomalie ou évolution caractéristique résultant d'un problème. Les phénomènes de dégradation et de contamination sont étudiés, au moyen de méthodes d’analyses de laboratoire ou bien à l’aide de méthodes rapide de contrôle, utilisées directement sur les sites industriels.
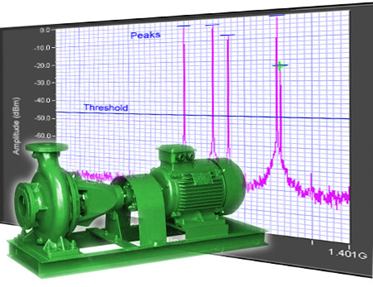
- Enseignant: Smail BENISSAAD